I’ve collected a number of dash plaques and was wondering what to do with them all. I did some quick research online and found that people either put them on their dash, threw them out, gave them away, stored them in a shoe box, or made some kind of display for them. I decided to mount them so that I could either show them with my car or hang them on the wall.
First I went to Target and purchased a poster frame. The one i bought was 18″ x 24″ and was less than $10. I probably should have picked a larger one but I didn’t want to invest a lot of money in case it didn’t work out. I also purchased some Scotch permanent mounting squares to mount the plaques to the frame. Several of the plaques already had double sided sticky tape on them but I used the mounting squares so the plaques would all be the same distance off of the board when mounted. In afterthought it may have looked interesting if the mounting depths had varied.
This is the poster frame I bought.
These are the mounting squares I bought.

The next step, arranging the plaques on the poster frame, was the most time consuming (at least for me). Before I mounted the plaques permanently, I laid them out on the frame so I could move them around and arranged them how I wanted. This took me quite a while before I found an arrangement that made me happy and was pleasing to the eye (at least in my opinion).
I started out arranging the plaques in chronological order. This left a lot of empty spaces. I moved the plaques around to make them fit better but still keeping the years together. This let me fit more of the plaques on the board, but there was still wasted space and leftover plaques. I decided to try arranging the plaques by car show. This let me fit most of my plaques on the board, but it looked unbalanced to me as all the large plaques were grouped together and all the smaller plaques were also grouped together.
The final arrangement I ended up with was to place the plaques randomly, trying to keep the years somewhat together and to not place plaques from the same show next to each other. This made for a more balanced looking arrangement and gave me the flexibility I needed to fit most of my plaques on one frame. I used the mounting squares to attach the plaques in the arrangement i had laid out. I had two very large plaques left over, so I saved them for my next frame after I collect more plaques.
This the arrangement I ended up with.
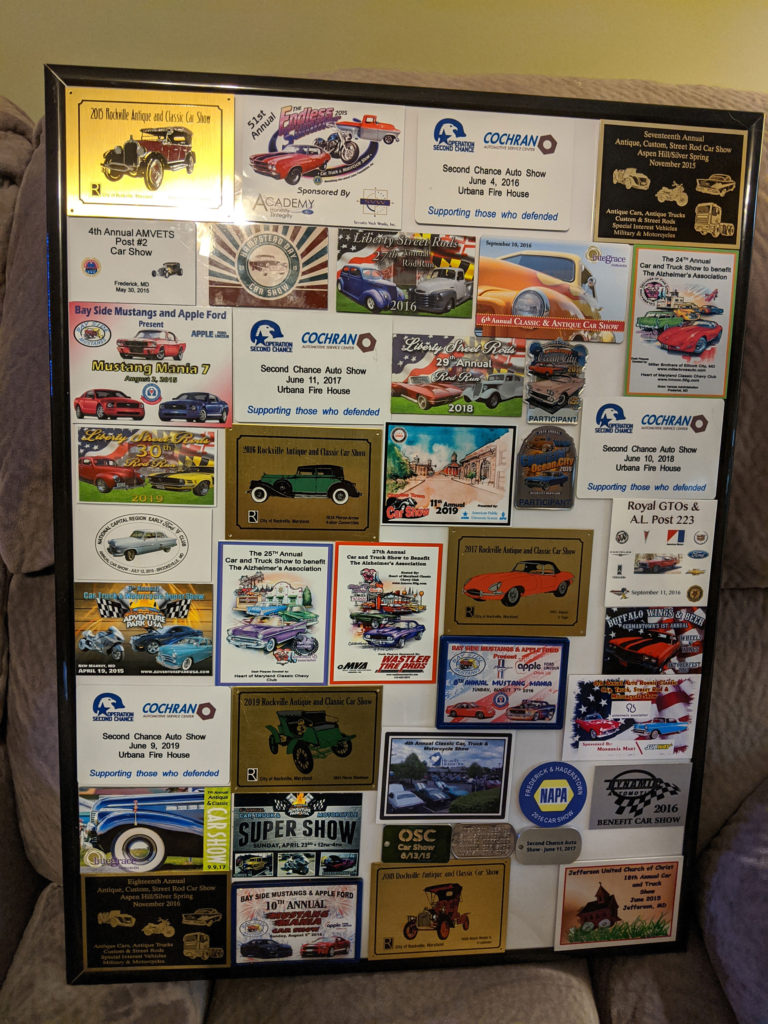